Every year millions of tyres are broken down into rubber crumb for the manufacture of other products such as athletic surfaces, rubberised asphalt and commercial flooring. Larger rubber crumb, which is typically processed to sizes ranging from 5 mesh to 30 mesh, is used for artificial sports fields and play surfaces.
There is also increasing global demand for commercial quantities of finer crumb or powder, such as 50 mesh material, which is about the size of table salt. Finer sizes can be mixed with recycled plastics to make plastic rubber pellets that can be injection moulded or extrusion moulded into a range of products. Drive Roller
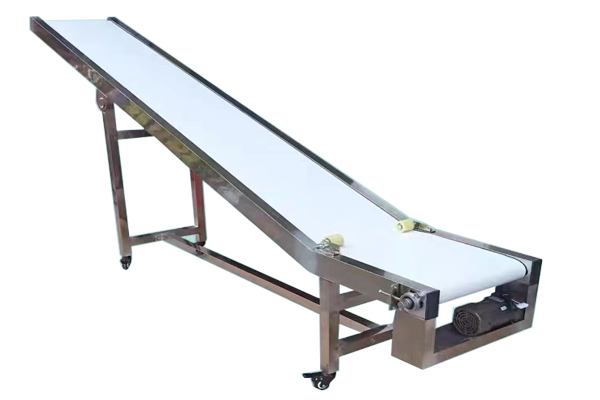
Even smaller crumb rubber can be used to make asphalt binding or mixed into roofing materials like epoxies, applications that tend to bring the highest value for the rubber material. As a result, tyre recyclers are looking for more productive milling machines, including alternatives to traditional gearbox-driven equipment, that can efficiently and cost-effectively grind these smaller particles.
These trends create challenges for many tyre recyclers because traditional gearbox-driven mills are generally built to process larger crumb sizes with the smaller crumb being a by-product. But this is not an efficient way to produce small crumb in large volumes. For example, the production of every 4kgs of 8 mesh to 18 mesh generates roughly 1kg of –20 mesh crumb. However, the amount of small crumb produced with traditional equipment is not enough to fulfil the growing need for the smaller materials. Eco Green’s Krumbuster allows the processor the flexibility to produce high volumes of both larger and smaller crumb sizes with minimal effort required to change nip (roller spacing), friction ratios, and roller corrugation design. This offers the best option for both large and small crumb rubber production.
Eco Green designed its patented Krumbuster fine grinding mill to process wire-free and fibre-free tyres, which had previously been processed into rubber chips of 6 mm or smaller, into rubber powder down to 0.850 mm and smaller, depending on the screening. The capability of this next-generation cracker mill to process rubber into finer material allows recyclers to take potentially unusable large crumb rubber and produce smaller, higher-value material that aligns with this upward demand.
‘Our mission has always been to make tyre processing equipment more efficient, as well as less expensive and easier to maintain,’ says Bruce Bart, Eco Green Equipment North American sales manager. ‘That’s what made our investment in developing this type of solution a natural evolution for our product line.’
Although the Krumbuster has evolved, the hydraulic grinding mill has always operated with two corrugated rollers, one small and one large, each powered by a compact and powerful Hägglunds CA 100 direct drive motor from Bosch Rexroth.
In a tyre grinding mill, each of the two rollers operates at a different speed to grind the rubber into usable crumbs. The speed differentials, or friction ratio, help determine the quality and size of the crumb being produced. One significant advantage to using Hägglunds direct drive technology is that it allows operators to run the rolls at much higher speeds than a gear-driven mill to produce a wider range of sizes, including smaller crumb.
Hägglunds technology also allows the Krumbuster to produce roughly 680kg to 800kg per hour of –30 mesh crumb, up to five times the additional material output per hour of a mechanical mill. According to Bart, ‘With the Krumbuster, our customers can run the roll so much faster using the Hägglunds motor, and then back down the speed of the other roller as well. That gives customers a high 80:1 friction ratio that’s simply not available with traditional gear-driven mills.’
One of the primary challenges in designing a mill for shredding applications is to account for shock loading. During production of crumb rubber, the mill is subject to varying levels of feed load into the system, which creates pressure drops or load spikes depending on how much or how little material is loaded. The drive must be able to respond to the shock load without undue wear and tear on drive components. Failure to compensate for this can lead to considerable costs from breakdowns and downtime.
The Hägglunds motor can better adapt to these shifts because it uses direct drive technology, in which the hydraulic motor is mounted directly to the drive shaft, eliminating the need for gear reducer, belts, chains or sprockets. The unique design delivers the full energy of operation to the shaft being driven and uses the hydraulic fluid as the medium to absorb the surges and drops, rather than having mechanical gears that lash in a gearbox system.
Hägglunds direct drive systems also offer superior speed and directional control compared to gearbox-coupled drive solutions. Since the variable flow of oil from the pump determines the speed and direction of the drive, speed and directional control are not compromised by the limitations of the electric motor. And due to the hydraulic motor’s low moment of inertia, the response is almost instantaneous. With this design, customers can feed material up to 7cm deep along the entire length of the Krumbuster roller. The motor’s resistance to shock loads and its ability to easily start, stop and reverse make it ideal for this type of application, which requires robust components.
In addition, the CA 100 consumes at least 30% less power than big mills, which often run direct drives up to 250 horsepower. ‘The efficiency of the Hägglunds motors helps optimise the efficiency of the entire system, much like a race car is built with optimal parts from each manufacturer,’ says Jaime Sabogal, market segment manager for Hägglunds.
An additional aspect for using Hägglunds, says Bart, is the simplicity and ease of maintenance. ‘Not having to replace gearboxes is always a good thing, and the reliability has been outstanding. We haven’t had many issues with Hägglunds but, when something does come up, their engineers work with us to resolve it very quickly. That makes us happy, and it makes our customers happy.’
Hägglunds’ long reputation for building reliable, quality motors also helps sell Eco Green products. ‘When people see photos of that orange motor in the brochure or see the machine itself at a trade show, they immediately recognise it’s a Hägglunds,’ adds Bart. ‘Even though our cracker mill has evolved over the years as we implement new technology improvements, the Hägglunds motor continues to be the best choice for powering all versions of our Krumbuster.’
Don't hesitate to contact us to share your input and ideas. Subscribe to the magazine or (free) newsletter.
Your email address will not be published. Required fields are marked *
This site uses Akismet to reduce spam. Learn how your comment data is processed.
How long has your company been in the recycling business?
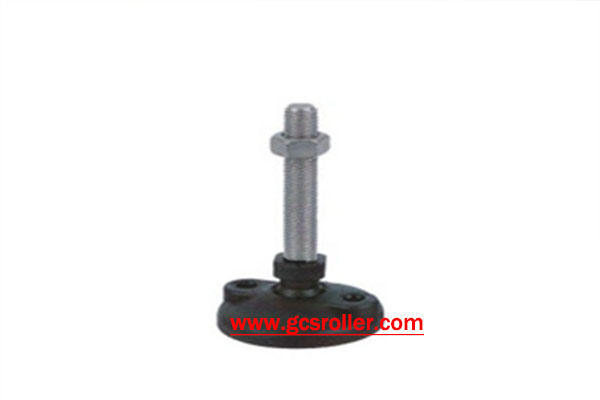
Friction Rollers Stay on top of developments across the markets with our weekly newsletter.