Haven't got an account?
Haven't got an account? Construction Air Compressor
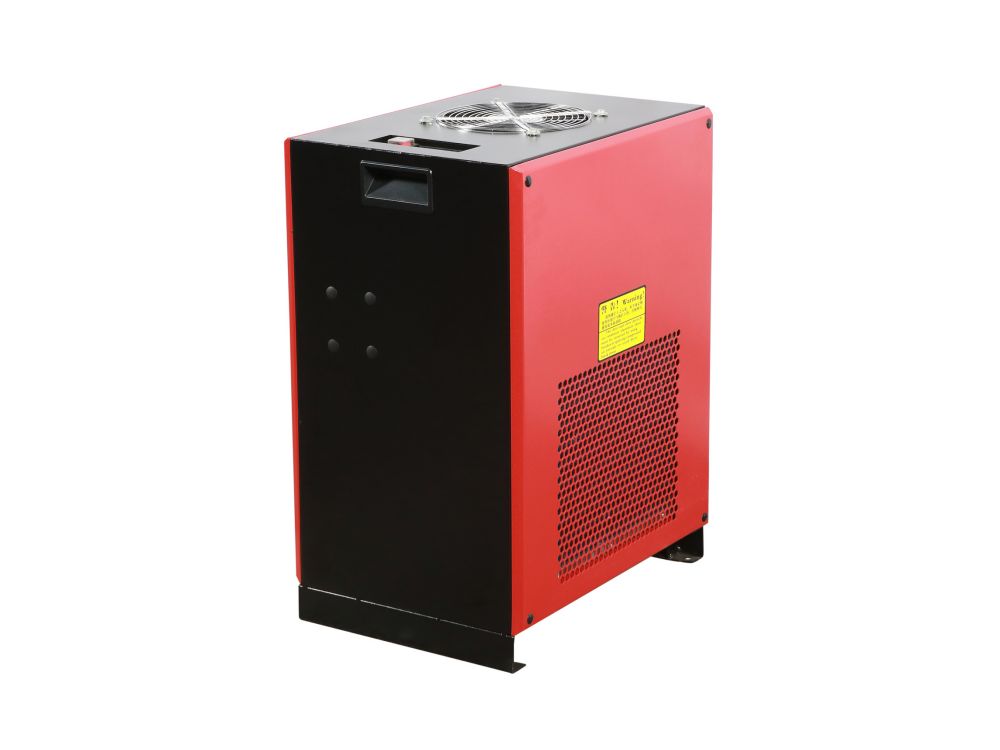
After reciprocating, sliding vane compressors, also referred to as rotary vane compressors, are one of the oldest types of compressors. The first known description of a sliding vane pump was in a book by an Italian engineer, Agostino Ramelli, written in 1588.
The rotary vane pump was patented June 16, 1874 by Charles C. Barnes, a Sackville, New Brunswick, Canada engineer who is generally credited with inventing the modern design. Rotary vane compressors and pumps have been produced since the early 1900s, and a number of companies have produced them by the thousands.
The rotary vane compressor uses centrifugal motion to compress air or other gas. The cylindrical rotor is located eccentrically in a stationary casing, such that it is closest to the cylindrical casing bore at the discharge port and farthest from it at the inlet port.
The casing has a large inlet and a comparatively smaller outlet or discharge port. The eccentric rotor has multiple radial slots, each of which is equipped with a blade or vane, which is spring-loaded. The vanes are made of steel or synthetic fiber materials. The springs and centrifugal force push the outer ends of the vanes against the housing bore to ensure that there is minimal gas leakage between adjacent vanes.
Depending on the application, the machines may be lubricated or non-lubricated. If the compressor is oil-lubricated, there will be a thin layer of oil between the vanes and the casing that also helps to seal against gas leakage past the vane tips during operation.
The space between adjacent vanes forms a pocket. As the eccentric rotor rotates in the cylindrical casing bore, each vane is displaced into its radial slot in the rotor. This progressively decreases the volume of the pocket between adjacent vanes as they rotate from the inlet to the discharge.
The decrease in volume increases the pressure of the trapped gas. Vane strength and leakage rate past the vane tips limits the differential pressure across a vane. Therefore, higher pressure ratio compressors require more vanes. A typical single stage rotary vane compressor has a pressure ratio of 5:1, with some high-pressure models as high as 7:1 or 8:1. The greater the number of vanes, the smaller the pressure difference between adjacent spaces around the rotor.
High-pressure ratio applications may require as many as 20 or 30 vanes. Most rotary vane compressors are limited to pressures of 150 psig (10.3 bar) or less. Although they are light weight and versatile, their efficiency is low compared to reciprocating compressors. Rotary sliding vane technology has been applied for air and gas compression, vacuum services, liquid pumping and transfer of bulk solids.
Blackmer was one of the first companies to develop sliding vane machines. Before the turn of the 20th century, a rotary pump was generally understood to be a “gear pump,” consisting primarily of two meshing gears which trapped liquid between the gear teeth and the pump housing, creating small sealing cavities that transported fluid as it rotated, forcing the liquid out the other side.
But in 1899, R. M. Blackmer came up with a vane-type pump design that was an important departure from the gear pump principle. In contrast to the flow rate from a gear pump that drops steadily as the gear teeth wear away, the loss from a vane-type pump is practically negligible. As the vanes wear away at the tips, they simply move further out of the rotor slots to self-adjust and maintain the original rate. Blackmer couldn’t have picked a better time to invent this ingenious type of pump.
The advent of the automobile was giving the country a new thirst for gasoline and oil. The petroleum industry was growing by giant strides and the young firm was prepared to expand with it. Blackmer’s vane pump fathered a family of hundreds of different pump models. The Blackmer company was founded in Petoskey, MI and moved to its current location in Grand Rapids, MI in 1925.
In 1908 Karl Wittig developed a patent in Germany for a sliding vane compressor with multiple vanes. Within five years he was licensing it as System Wittig. Wittig rotary vane compressors and vacuum pumps were used in many applications and continue today as part of Gardner Denver with niches in dry bulk, liquid and gas transfer and vacuum services.
In 1930, Allis-Chalmers of Milwaukee, WI was one of the earliest companies to adapt the rotary vane technology to compressor applications. Its Ro-Flo rotary vane compressor was originally developed as a plant air compressor, but it gradually found applications in compressing wet and sour gases.
Allis-Chalmers products changed hands over the ensuing years, but the Ro-Flo product survived and Ro-Flo Compressors became an independent company in 2007. Ro-Flo compressors evolved into some of the higher capacity machines in the industry, operating to 200 psig with up to 7:1 pressure ratio in a single stage.
James W. Fuller III founded a company in Lehigh Valley, PA in 1926. Beginning as a foundry, he soon designed specialized products and processes for the cement and other industries. To help customers in the loading and unloading of materials, he acquired the rights to a French multi-vane rotary compressor design in 1931.
He developed the technology for both vacuum pump and compressor applications. Compared to reciprocating compressors, the new vane design was compact, had negligible vibration and was pulsation-free. Since 1990, Fuller compressors have been a product of FLSmidth.
Rotary vane compressors and pumps have been used in hundreds of different applications. In addition to providing compressed air, rotary vane compressors are used to move bulk solids and transfer liquids. They are used in oil and gas applications, industrial gas production, vapor recovery and vacuum services.
They have also been commonly used in vehicles for engine supercharging, air conditioning and power steering compressors and automatic transmission pumps. They can be designed to handle almost any gas imaginable, including acid and sour gas, hydrogen and heavy hydrocarbons
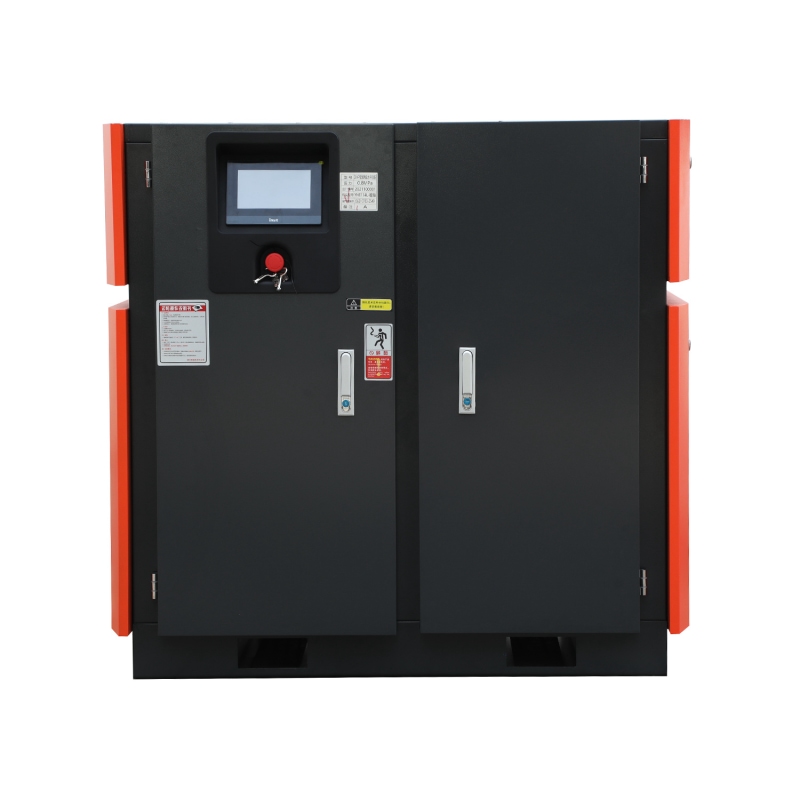
Air Dryer Working Since they can handle bi-phase flow, they are also used for compressing gas streams which are near their dew point and have liquids present.